Contact us today for all your air gaging needs! (801) 716-2972
Gage-Lab Products is partnered with Edmunds gages to bring you precision air gaging tools. Edmunds has developed a two-master, back-pressure bleed system, which is the most accurate air gaging method to use.
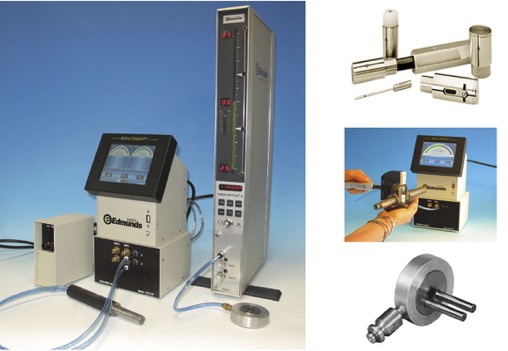
Air gaging is a technology that employs the use of air flow volumes and air pressure to determine the size of measured part dimensions. To achieve this measurement, it relies on the laws of physics, which state that flow and pressure are directly proportionate to clearance and react inversely to each other. As clearance increases, air flow also increases and air pressure decreases proportionately. As clearance decreases, air flow also decreases and air pressure increases accordingly.
Click HERE for a detailed air gaging brochure.
Air Gaging Applications:
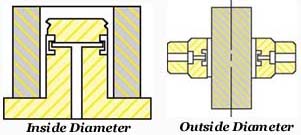
Inside and Outside Diameters
Air gages are most commonly used for measuring the size and form of inside diameters (IDs) and outside diameters (ODs). Two-nozzle air plugs, with nozzles diametrically opposed, are often used for internal measuring, and two-nozzle air rings are used for external dimensions.

Multiple nozzles are equally located about the circumference of the air tool to allow for average size measurement. Commonly used for thin-walled or out-of-round parts – four, six, or more nozzles are used, depending on the tool size.
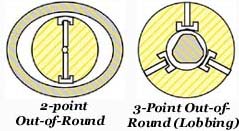
Out-Of-Round
Air tools can gage a part for roundness. For two-point out-of-round conditions, a standard two-nozzle air tool can be used. If lobing exists in the part, an odd number of nozzles must be used, depending on the number of lobes.
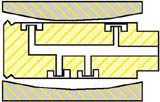
A common application of air gaging is to dynamically measure the straightness or "bow" of an ID. In this case, a custom-designed air plug makes verifying a part's straightness simple and fast. (A straightness air plug cannot measure diameter).
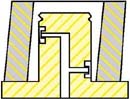
Squareness
To determine squareness of a part, for example a bore to face, air nozzles configured as a "z" are used with dynamic measurement to change the back pressure from square to out-of-square conditions.

Angle variation of tapered surfaces is commonly checked with air gaging as the difference of two diameters.
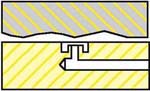
To measure flatness, an air nozzle is mounted within a stationary platen. The part is then moved across the nozzle. This process provides a convenient, quick method to accurately gage flatness.
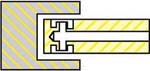
The measurement of grooves is conveniently achieved with flat, blade-type air tools. Air gaging not only determines groove size, but with exploration around the workpiece, parallelism of the groove faces can also be determined.
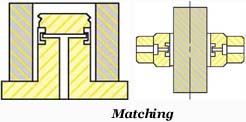
A specified clearance between two mating parts is often required to assure proper part operation. An amplifier allows for the individual display of the bore size, the shaft size, and the clearance between the two parts. Operators need only observe the clearance display to determine if the two components have the required match
Air Gaging vs. Contact Gaging
Contact gaging measures the dimension from surface roughness peaks of the part being measured (i.e. at plane A - A).
Open nozzle air gaging measures the mean surface of the part, which is approximately the average of surface finish peaks and valleys (i.e. at plane B - B). Technically, the mean surface would be an imaginary plane established by using the material from the peaks to fill the valleys until a level or zero line is formed.
The result is that there is a difference in measurement between air gaging and contact gaging. The amount of this difference is a function of surface roughness. The inside diameter of a hole will read larger with an air gage than it will if measure with a contact gage. Conversely, the outside diameter of a shaft will read slightly smaller with an air gage.
The following chart shows the diametral difference between air gaging and contact gaging:
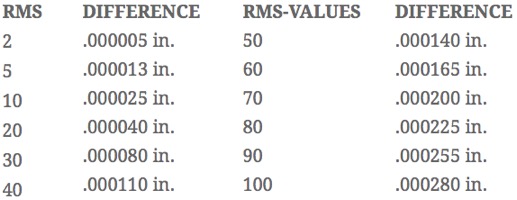
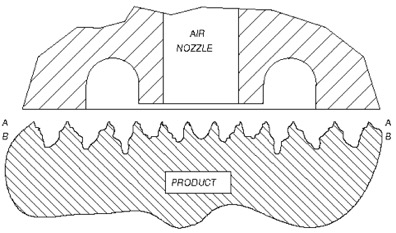